Strategies for Implementing Continuous Improvement Projects
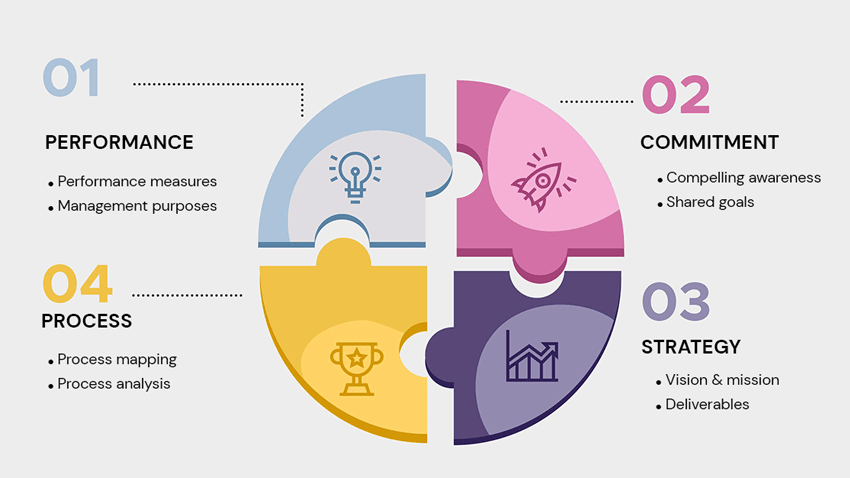
Certainly! Here are some additional examples of continuous improvement practices that you can implement on your shop floor:
1. Kaizen Events:
- Conduct regular Kaizen workshops or events. These involve cross-functional teams identifying and solving specific problems within a short timeframe. - Focus on a specific process, area, or issue, and encourage employees to brainstorm solutions together.
2. Standard Work Procedures:
- Develop and document standard operating procedures (SOPs) for critical processes. - Regularly review and update these procedures based on feedback and lessons learned.
3. Visual Management:
- Use visual cues to communicate information effectively: - Visual boards: Display key metrics, goals, and progress. - Color-coded labels: Organize materials and tools for easy identification. - Floor markings: Guide movement and placement of items.
4. Error-Proofing (Poka-Yoke):
- Implement mechanisms to prevent errors at the source: - Checklists: Ensure critical steps are followed. - Jigs and fixtures: Guide correct assembly or positioning. - Color-coding: Differentiate components or parts.
5. Gemba Walks:
- Regularly visit the shop floor (known as Gemba) to observe processes firsthand. - Engage with employees, ask questions, and identify improvement opportunities.
6. Cross-Training:
- Train employees to perform tasks outside their usual roles. - This enhances flexibility, reduces dependency, and promotes a deeper understanding of the entire process.
7. Andon Systems:
- Install visual alert systems (such as lights or displays) to signal abnormalities or issues. - When a problem occurs, workers can activate the Andon to seek immediate assistance.
8. Value Stream Mapping:
- Map out the entire value stream for a product or process. - Identify areas of waste (e.g., waiting, excess inventory) and streamline the flow.
9. Employee Suggestions:
- Encourage employees to submit improvement ideas. - Set up a system for collecting, evaluating, and implementing these suggestions.
10. Quality Circles:
- Form small groups of employees who meet regularly to discuss quality-related issues. - Collaborate on problem-solving and share best practices.
Remember that continuous improvement is not a one-time effort; it's an ongoing journey. Involve your team, celebrate successes, and adapt as needed to create a culture of excellence! 🛠️🌟
0 Comments