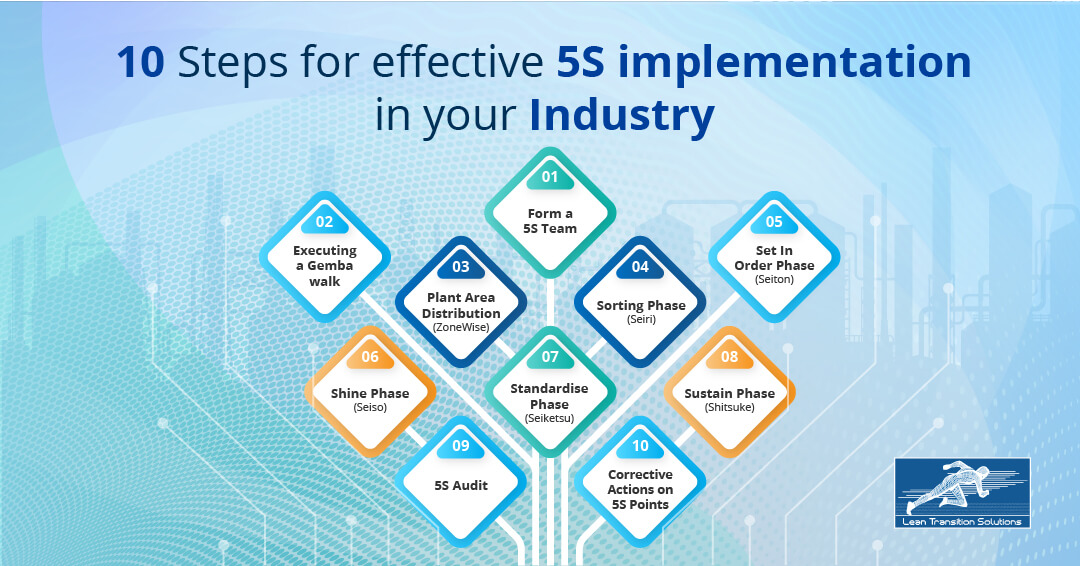
5S Implementation Steps for Improved Workplace Efficiency
The 5S methodology is a powerful tool for improving workplace organization, cleanliness, and overall efficiency. By following these ten simple steps, you can create a safer, more productive, and more enjoyable work environment for everyone.
The 5S Steps:
- Form a 5S Team 1 Assemble a dedicated group to oversee the 5S implementation process.
- Executing a Gemba Walk 2 Observe the current workplace layout and identify areas for improvement.
- Plant Area Distribution (ZoneWise) 3 Divide the workspace into designated zones for easier organization.
- Sorting Phase (Seiri) 4 Eliminate unnecessary items like old tools, machinery, or materials.
- Set In Order Phase (Seiton) 5 Organize remaining items for easy access and use. Label shelves, drawers, and create designated storage areas.
The 5S Steps (Continued):
- Shine Phase (Seiso) 6 Clean the workplace regularly and maintain a hygienic environment.
- Standardize Phase (Seiketsu) 7 Establish clear procedures and protocols for maintaining the organized and clean workspace.
- Sustain Phase (Shitsuke) 8 Foster a culture of continuous improvement by encouraging regular upkeep and addressing any deviations from the established standards.
- 5S Audit 9 Conduct regular inspections to ensure adherence to the 5S principles and identify areas for further improvement.
- Corrective Actions on 5S Points 10 Implement corrective actions to address any issues identified during the 5S audit and maintain a consistently organized and efficient workspace.
By implementing the 5S methodology, you can expect to see improvements in several key areas, including:
- Increased productivity: Reduced time spent searching for tools and materials.
- Improved safety: Reduced clutter and a cleaner environment minimize safety hazards.
- Enhanced quality: Consistent organization helps maintain quality standards.
- Boosted morale: A clean and organized workspace creates a more positive work environment.
- Reduced waste: Eliminating unnecessary items minimizes waste and associated costs.
0 Comments